Unlocking Investment Opportunities in Robotic MIG Welding: A Future-Proof Solution for Modern Manufacturing
- MBIM
- Apr 12
- 4 min read
Updated: Apr 24
In today’s manufacturing environment, automation has become a necessity rather than a luxury. As the automotive, shipbuilding, and aerospace industries strive to meet rising demands for quality, efficiency, and safety, robotic welding has emerged as a cornerstone of modern production. Robotic MIG (Metal Inert Gas) welding stands out for its precision, productivity, and versatility among the various welding technologies. For investors and manufacturers alike, this innovative solution presents a compelling opportunity to drive profitability, enhance competitiveness, and prepare for an automated future. This article explores the advantages of robotic MIG welding, its edge over alternatives like TIG welding, the growing role of collaborative robots (cobots), and why it’s a smart investment in today’s market.
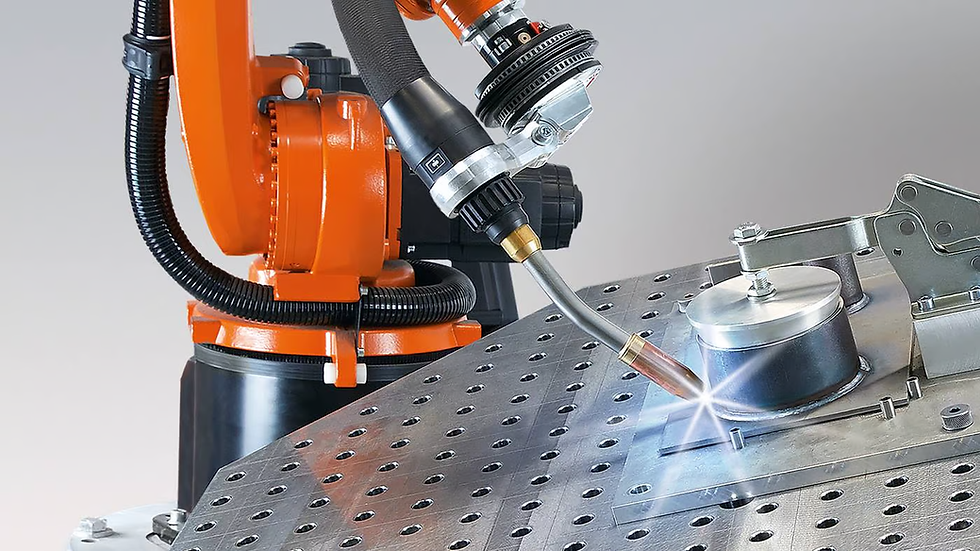
The Power of Robotic MIG Welding: Key Advantages
Robotic MIG welding is revolutionising manufacturing by delivering a suite of benefits that address the core needs of modern production. Here’s why it’s becoming indispensable across industries:
Unmatched Precision and Consistency: Robotic MIG welding systems ensure every weld is identical, minimising defects and maintaining high-quality standards. Capable of navigating complex weld paths and reaching difficult areas, these systems reduce rework, saving time and resources. For instance, a heavy equipment manufacturer can rely on MIG welding to join thick steel plates quickly and durably, while automotive producers benefit from consistent vehicle frame welds that meet stringent safety requirements.
Increased Efficiency and Productivity: Automation accelerates welding cycles with consistent speeds, slashing production times. Unlike human welders, robots operate 24/7 without breaks, boosting throughput. Integration with other automated systems further streamlines workflows, making robotic MIG welding a powerhouse in high-volume sectors like appliance production.
Cost-Effectiveness Over Time: While the initial investment may be significant, the long-term savings are substantial. Precise welds use less filler material, and fewer errors cut costs tied to rework or scrap. A mid-sized fabrication shop, for example, could recoup its investment within a few years through labour savings and enhanced output.
Enhanced Worker Safety: Welding hazards—burns, toxic fumes, and eye damage—are mitigated as robots handle the work, allowing operators to monitor from a safe distance. By taking on repetitive tasks, robots also reduce worker fatigue and injuries, a critical advantage in shipbuilding where large welds in confined spaces are routine.
Versatility Across Applications: From steel to aluminium, robotic MIG welding systems adapt to various materials and weld types, meeting diverse production needs. This flexibility makes them ideal for applications ranging from automotive assembly to machinery fabrication.
These advantages position robotic MIG welding as a transformative technology that not only meets today’s demands but also prepares businesses for future challenges.
MIG vs. TIG Robotic Welding: Why MIG Takes the Lead
When choosing a robotic welding method, the decision between MIG and TIG (Tungsten Inert Gas) welding hinges on productivity, quality, and automation feasibility. While both have strengths, MIG often emerges as the superior choice for robotic applications:
Strengths of MIG: MIG welding is highly effective for joining thicker metals, as it uses filler material to achieve deep penetration and maintain structural integrity. Its continuous wire feed allows for faster deposition rates, making it ideal for high-volume production in applications such as automotive assembly or structural steel fabrication. Moreover, robotic MIG welding produces high-quality welds with minimal spatter and attractive weld beads, which reduces the need for post-weld finishing. Additionally, its versatility allows it to be used in various positions, e.g. flat, horizontal, vertical, or overhead, which is essential for complex assemblies like ship hulls.
Limitations of TIG: TIG welding offers precision for specialised tasks, but its complexity hinders automation. Robotic TIG, while more efficient than manual TIG, lags behind MIG in ease of automation and productivity. Challenges include managing intricate settings, manoeuvring bulky torches in tight spaces, and slower wire feeding speeds. Frequent adjustments and tungsten electrode erosion add further complexity, making TIG less cost-effective for many robotic applications.
For manufacturers prioritising throughput and efficiency, robotic MIG welding provides a simpler, more productive solution without compromising quality, a key factor driving its adoption.
The Rise of Cobots: Enhancing Flexibility and Accessibility
Collaborative robots, or cobots, are reshaping the welding landscape by combining automation’s power with human collaboration.
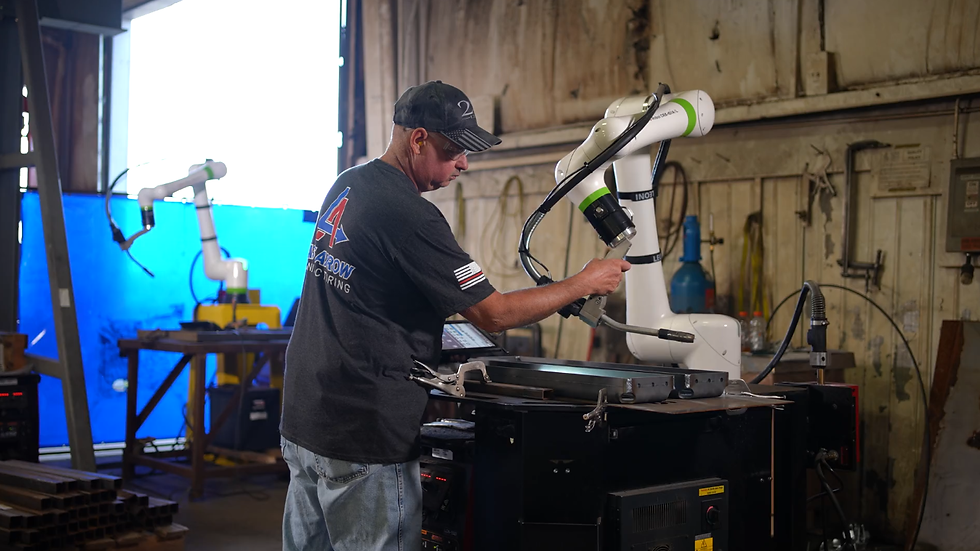
Unlike traditional robots confined to isolated setups, cobots work safely alongside operators, offering unique advantages:
Flexibility: Cobots are easily reprogrammed and redeployed, making them ideal for high-mix, low-volume production environments—situations where traditional robots struggle. This adaptability suits manufacturers handling varied designs.
Ease of Use: User-friendly interfaces, such as smartphone apps or teach pendants, allow even non-specialised staff to operate cobots, lowering the skill barrier and broadening their appeal.
Enhanced Productivity: Custom parameters, such as precise torch angles and optimised travel speeds, enhance efficiency. A case study of a custom stainless-steel component manufacturer highlights this: after deploying a welding cobot, productivity rose 30% due to seamless task-switching without extensive reprogramming.
As cobot technology advances with features like real-time adaptive sensors and Industry 4.0 integration, their role in MIG welding is set to grow, offering investors a dynamic entry point into automation.
Investment Opportunities: A Growing Market with High Returns
The global robotic welding market is on an upward trajectory, fuelled by demand for efficiency, quality, and safety in manufacturing. Industries like automotive, aerospace, and metal fabrication are leading the charge, adopting robotic MIG welding to stay competitive. For investors, this technology offers tangible benefits:
Increased Throughput: Faster cycles and continuous operation drive higher output, meeting market demands efficiently.
Reduced Labour Costs: Automation eases reliance on skilled welders—a scarce resource—lowering operational expenses.
Improved Product Quality: Consistent, high-quality welds enhance reliability and customer satisfaction, strengthening brand reputation.
Long-Term Savings: Despite upfront costs, reductions in material waste, rework, and labour yield a strong return on investment (ROI). Industry reports suggest the robotic welding market will expand significantly in the coming years, amplifying these gains.
Technological advancements, such as AI-driven sensors and smart manufacturing integration, further enhance robotic MIG welding’s appeal, promising greater efficiency and adaptability. For businesses, investing in this technology is a strategic move to secure a foothold in an automated future.
Conclusion: A Smart Investment for Tomorrow’s Manufacturing
Robotic MIG welding is more than a technological upgrade—it’s a gateway to manufacturing excellence. Its precision, efficiency, cost-effectiveness, safety, and versatility make it a vital asset for industries facing rising competition and complexity. As automation continues to dominate, adopting robotic MIG welding will accelerate, offering investors and manufacturers a chance to boost productivity, cut costs, and lead their markets. By embracing this future-proof solution, businesses can not only thrive today but also position themselves for tomorrow's opportunities.
Comments